The Type Of Fmea Used For A Product Before Going Into Manufacturing Is A ___________ Fmea.
Jump to: How Exactly Do You Pronounce FMEA? What are the Types of FMEA? How Does a FMEA Process Work? The Steps to Perform a FMEA What is a DFMEA or Design FMEA? What is a PFMEA or Process FMEA? What is a FMECA? Other FMEA Types Automating with FMEA Software
PROCESS FMEA (PFMEA) The Process FMEA is normally used to analyze manufacturing and assembly processes at the system, subsystem or component levels. This type of FMEA focuses on potential failure modes of the process that are caused by manufacturing or assembly process deficiencies. Although Design FMEAs are used to analyze medical equipment. Process FMEA Analysis is at the manufacturing/assembly process level. The Focus is on manufacturing related deficiencies, with emphasis on Improving the manufacturing process ensuring the product is built to design requirements in a safe manner, with minimal downtime, scrap and rework. Manufacturing and assembly operations, shipping.
FMEA, or Failure Mode and Effects Analysis, is an organized, systematic approach for assessing potential system failures and the resulting consequences of those failures. The objective of a FMEA is to evaluate the risk associated with the identified failure effects and come up with a plan to detect, prevent, or mitigate those deemed most critical. Overall, FMEAs provide an invaluable approach for maintaining and improving your reliability and quality objectives. It is why FMEAs consistently remain one of the most used methodologies in corporate reliability and quality efforts.
In the post, we’ll help provide an overview of the different types of FMEAs and provide FMEA examples to help you understand the purpose and use of FMEAs.
First…How Exactly Do You Pronounce FMEA?
Types Of Fmea Pdf
The term “FMEA” is sometimes pronounced simply by spelling out the letters of the acronym: “F”, “M”, “E”, “A”. Usually, it is pronounced as a word: “Fah-Me-Ah”. Sometimes “Fee-Mah” is heard, but this tends to be confusing because it more commonly applies to the Federal Emergency Management Association (FEMA).
Because there are various types of FMEAs, sometimes a qualifier prefix may be used. For example, Design FMEAs can be referred to as “D” FMEAs, and Process FMEAs as “P” FMEAs. In general, the term FMEA can apply to the broad scope of any type of FMEA analysis, but if you want to be specific, you can use the prefixes.
Additionally, the acronym FMECA stands for Failure Mode, Effects, and Criticality Analysis. In most cases this is pronounced as the three-syllable “Fah-Me-Kah”. You can also spell out all 5 letters, but that tends to get a bit long!
What are the Types of FMEA?
There are a variety of FMEA types; however, all are focused on the same function of risk assessment and the detection, elimination, and/or mitigation of critical risk events.
The primary types of FMEAs include:
- System / Functional FMEAs
- Design FMEAs
- Process FMEAs
- Service FMEAs
- Software FMEAs
- Manufacturing FMEAs
How Does a FMEA Process Work? The Steps to Perform a FMEA
The steps to complete a FMEA remain essentially the same across all FMEA types.
- First, you break down your system, design, or process into its component elements – as granular or as high-level as you prefer.
- From that point, you systematically go through each element and determine all the possible ways it can potentially fail.
- For each failure, you analyze the effects and the likely causes of that failure.
- You then proceed to rank each potential effect based on the risk criteria of your choosing. For example, you may consider such items as severity (how critical is it), its occurrence (how likely it is to occur), and detection (how likely it would detected). There are several standard methods to quantify risk level – such as RPN (Risk Priority Number) calculations that measure risk on a 1-1000 scale, and Criticality, which is a computed metric based on actual probability values. You can customize risk assessment criteria to best fit your needs.
- Once the potential risk levels are ranked, you delve in to the important part of the analysis – determining how to minimize, detect, eliminate, or mitigate those you deem most critical. Typically, analysts then define a plan of recommended actions to implement in order to keep failure effect risks low.
- You then go back and determine your revised risk levels based on completed action items to ensure you have met your risk goals.
As you can see from the description of the procedure, FMEAs are best performed collaboratively with a team of engineers and analysts across all elements of the product or process lifecycle – from design, to development, to production, and to deployment. FMEA documents are best utilized as living documents so that the product, process, or system is evaluated throughout the lifecycle to maintain and continuously improve reliability and quality.
For a walk-through FMEA example, see A Real World Example in Six Steps.
What is a DFMEA or Design FMEA?
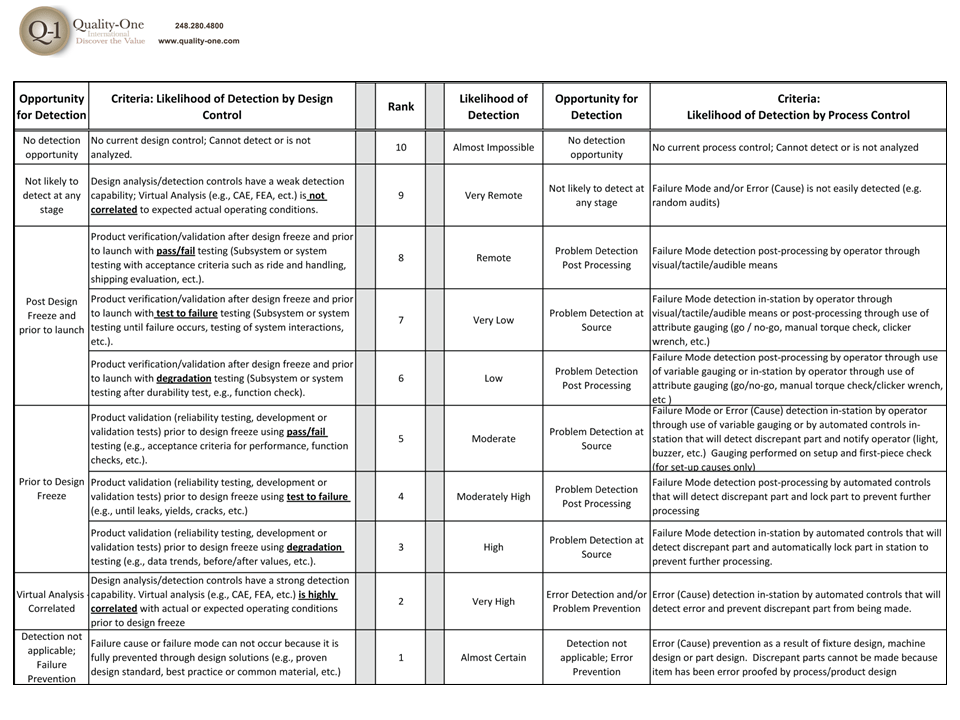
Design FMEAs, or DFMEAs, enable you to assess and address potential failure modes during the early or end stage of product design. When performing a Design FMEA, you begin by defining the system hierarchy, or the breakdown of all the individual components of your product. The breakdown can be as detailed as you like. For example, you may start your DFMEA early in the design phase when a high-level breakdown is available, and then as your design matures, continue to refine that breakdown into lower level elements.
Once your product design is broken down into components, you analyze the potential failure modes of each element. You then follow the remaining steps of the FMEA procedure as described earlier.
The steps of the DFMEA process include:
- Breakdown your system in a hierarchical format.
- Analyze the possible failure modes of each element in your system breakdown.
- Analyze the effects and causes of each failure.
- Rank the relative risk of each failure effect according to a criteria you prefer.
- Assign action items as needed to mitigate, eliminate, or detect high risk items.
- Go back and revise your risk levels based on completed actions.
- As your design matures, revisit your system breakdown to refine further and repeat steps 2 though 6.
What is the purpose of a Design FMEA?
DFMEAs are use to analyze a product during the design stage. Their main purpose is to ascertain and mitigate critical effects of failures prior to manufacture and deployment.
Cost of Defect Correction Across the Product Lifecycle
In the product lifecycle, the cost of correcting a failure dramatically increases along every stage of a product’s life. Correcting a problem while in the design, or “paper” stage, is minimal – you reassess the design and make appropriate changes to the design documents. Your cost is limited to the engineering time for redesign. Moving onto production, if a problem is uncovered, the resulting costs go up tremendously. Production shutdown, re-engineering, retest, and restarting production are costly and ineffective. Lastly, failures uncovered in the field are the most costly. You may be facing recalls, product replacement, and repairs, as well as all the costs associated with determining the root cause and necessary corrective actions. Add to that the almost immeasurable cost of harm to your reputation and company standing, and you can see why eliminating problems early on is key to business success.
What is DVP&R?
DVP&R is an acronym for Design Verification Plan and Report. DVP&R analysis is sometimes used in conjunction with Design FMEAs.
The purpose of DVP&R is to manage and document your tasks associated with verifying that your product meets design requirements. Your design specifications or product requirements are listed in the DVP&R Worksheet along with the tests used to verify that your requirements and/or specifications have been met – the Plan portion of DVP&R. Once the tests are performed, the results are recorded – the Report portion of DVP&R. You can track pass and fail testing, as well as keep track of progress and issues that may arise.
DVP&R is a tool that ensures you have an organized approach to validation of product design, provides feedback to know how well your design is progressing in relation to verifying it meets requirements, and maintains all this information in a central place for efficiency and future design iterations.
Example DVP&R Worksheet
Benefits Of Fmea
What is a PFMEA or Process FMEA?
Process FMEAs are used to analyze and maintain process control objectives. Essentially, PFMEAs are performed on a process as opposed to a product as with DFMEAs. The central component of a PFMEA is the PFMEA Worksheet, which can look very similar to a DFMEA Worksheet. In the initial columns of a PFMEA Worksheet you will break down the steps of your process instead of the components of your product as you would in a DFMEA.

You then follow the same FMEA procedure:
- Identify all potential failure modes of the process steps
- Determine the resulting effects
- Perform a risk assessment
- Define a plan for recommended actions for risk mitigation.
Oftentimes, PFMEAs are used in conjunction with Process Flow Diagrams (PFDs) and Process Control Plans (PCPs or CPs).
What is a Process Flow Diagram?
A Process Flow Diagram, or PFD, as indicated in the name, is a diagram, or visual view of a process. The PFD shows the flow of the process or equipment that is under analysis. Elements of a PFD resemble those of a flowchart, or flowsheet. This graphical view allows the overall process to be easily understood and grasped. Typically, there is a start node and an end node and then the interim blocks indicate the process steps to be analyzed.
PFDs include information based on your process requirements and specifications, such as product and process characteristics. This allows you to track and manage your requirements to ensure they are all met, and that all elements of your specifications are covered in your analysis.
Once the PFD has been defined, the next step is to perform your PFMEA.
The Central Part of PFMEA: The PFMEA Worksheet
The PFMEA Worksheet shares the process steps delineated in the PFD. You consider each process step and determine the potential failure modes associated with each one. The remaining portions of the analysis are then completed: determine the effects of the failure modes, assess the risks of those effects, and then the actions required to eliminate or mitigate those effects.
Example PFMEA Worksheet
Once the PFMEA Worksheet is completed, or mostly completed, the next phase is to work on the Process Control Plan.
What are Control Plans Used For?
The Process Control Plan (PCP), or Control Plan (CP), details the methods you will use to control the product and process characteristics to ensure they meet your quality requirements. The CP is used as an organized, detailed plan for documenting all the controls put in place to address all the failure issues identified in your PFMEA. Ultimately, the CP can be used to create operator instructions.
As in your PFMEA Worksheet, the CP shares the process steps defined in your PFD. The process steps, product characteristics, and process characteristics are the linking mechanisms across all elements of the PFMEA process – from PFD, to PFMEA, to CP.
You do not have to use all elements – PFD, PFMEA Worksheet, and CP – you can use just one, two, or all three. Whichever you choose, the process steps are a critical element tying the components of your PFMEA together, so care should be taken when defining those steps. Almost all PFMEAs use the PFMEA Worksheet. Depending your needs, you may decide to include a PFD and CP as well.
What is a FMECA?
FMECA, or Failure Mode, Effects, and Criticality Analysis, incorporates a specific type of criticality analysis in to the FMEA. Typically, FMECAs are performed based on the MIL-STD-1629A standard that defines a well-known and widely accepted procedure for FMEA. One of the defining characteristics of a FMECA (versus a FMEA) is the way criticality is assessed.
With MIL-STD-1629A FMECAs, you can use either a qualitative or quantitative approach to criticality assessment. With the qualitative method, the severity level of each potential failure effect is determined, along with the likelihood of occurrence of the failure mode. A criticality matrix, or graph, of severity versus occurrence is then used to evaluate risk level.
Using the qualitative method, first the Mode Criticality is computed as:
Item Unreliability x Mode Ratio x Probability of Loss x Operating Time
The Item Criticalities are then the sum of the Mode Criticalities. The resulting criticalities are then easily ranked based on their computed numeric value.
Another unique aspect often associated with FMECA is the level of system breakdown. FMECAs are often performed at the piece-part level. Konica c258 brochure pdf. Piece-part FMECAs break down a system into component subassemblies, and then down to the device level. This means that each device in the system, down to each integrated circuit (IC), resistor, capacitor, etc., is outlined in the FMECA Worksheet. At the device level, you then consider each possible failure mode and its resulting effects on its parent component, and then ultimately on the system. Piece-part FMECAs are highly detailed, very organized, and exceptionally comprehensive.
Example piece-part FMECA
Other FMEA Types
There are various other types of FMEAs, all which follow that same basic FMEA procedure and are used to assess and mitigate risk. In addition, organizations frequently create their own custom FMEAs to best suit their unique requirements. Oftentimes, companies begin with a FMEA standard as a starting point and then adapt and customize it as needed. Some commonly used FMEA standards include SAE J1739, ARP5580, AIAG, and MIL-STD-1629A.
Some other FMEA types include:
- Functional FMEAs, sometimes referred to as System FMEAs, analyze the functions of a system. For example, before a design is finalized, you can use the functional requirements as a basis to perform a Functional FMEA.
- Software FMEAs are performed by analyzing the ways software can fail and what the resulting effects of those failures are on the system. As the breadth and depth of software dramatically increases in today’s systems, Software FMEAs can be vitally important to address all potential failure paths.
- Service FMEAs are unique in that they analyze a service you plan to provide or create in order to meet a customer’s needs.
- Manufacturing FMEAs are similar to process FMEAs in that they analyze the potential failures associated with a manufacturing process.
Automating Failure Mode & Effects Analysis with FMEA Software
For overall efficiency, it is best to use a tool expressly built for performing FMEAs. You get the advantages of data sharing, reusability, built-in criticality and risk calculations, and support for team collaboration.
Because FMEAs are best performed as a team effort, selecting a FMEA tool that supports ease of collaboration, including web-friendly and mobile-friendly features, can be most effective.
Relyence FMEA was designed and built to meet all the needs of FMEA analysts. Supporting the most widely accepted standards with complete customization capabilities, along with powerful features for team collaboration, Relyence FMEA is the proven go-to tool for Failure Mode and Effects Analysis.
Feel free to contact ustoday to discuss your FMEA needs, or see Relyence FMEA in action today with a free trial!
Also called: potential failure modes and effects analysis; failure modes, effects and criticality analysis (FMECA).
Begun in the 1940s by the U.S. military, failure modes and effects analysis (FMEA) is a step-by-step approach for identifying all possible failures in a design, a manufacturing or assembly process, or a product or service. It is a common process analysis tool.
- “Failure modes” means the ways, or modes, in which something might fail. Failures are any errors or defects, especially ones that affect the customer, and can be potential or actual.
- “Effects analysis” refers to studying the consequences of those failures.
Failures are prioritized according to how serious their consequences are, how frequently they occur and how easily they can be detected. The purpose of the FMEA is to take actions to eliminate or reduce failures, starting with the highest-priority ones.
Failure modes and effects analysis also documents current knowledge and actions about the risks of failures, for use in continuous improvement. FMEA is used during design to prevent failures. Later it’s used for control, before and during ongoing operation of the process. Ideally, FMEA begins during the earliest conceptual stages of design and continues throughout the life of the product or service.
When to Use FMEA
- When a process, product or service is being designed or redesigned, after quality function deployment (QFD).
- When an existing process, product or service is being applied in a new way.
- Before developing control plans for a new or modified process.
- When improvement goals are planned for an existing process, product, or service.
- When analyzing failures of an existing process, product, or service.
- Periodically throughout the life of the process, product, or service
FMEA Procedure
Note: This is a general procedure. Specific details may vary with standards of your organization or industry. Before undertaking an FMEA process, learn more about standards and specific methods in your organization and industry through other references and training.
- Assemble a cross-functional team of people with diverse knowledge about the process, product or service, and customer needs. Functions often included are: design, manufacturing, quality, testing, reliability, maintenance, purchasing (and suppliers), sales, marketing (and customers), and customer service.
- Identify the scope of the FMEA. Is it for concept, system, design, process, or service? What are the boundaries? How detailed should we be? Use flowcharts to identify the scope and to make sure every team member understands it in detail.
- Fill in the identifying information at the top of your FMEA form. (Figure 1 shows a typical format.) The remaining steps ask for information that will go into the columns of the form.
Figure 1: FMEA Example
- Identify the functions of your scope. Ask, “What is the purpose of this system, design, process, or service? What do our customers expect it to do?” Name it with a verb followed by a noun. Usually one will break the scope into separate subsystems, items, parts, assemblies, or process steps and identify the function of each.
- For each function, identify all the ways failure could happen. These are potential failure modes. If necessary, go back and rewrite the function with more detail to be sure the failure modes show a loss of that function.
- For each failure mode, identify all the consequences on the system, related systems, process, related processes, product, service, customer, or regulations. These are potential effects of failure. Ask, “What does the customer experience because of this failure? What happens when this failure occurs?”
- Determine how serious each effect is. This is the severity rating, or S. Severity is usually rated on a scale from 1 to 10, where 1 is insignificant and 10 is catastrophic. If a failure mode has more than one effect, write on the FMEA table only the highest severity rating for that failure mode.
- For each failure mode, determine all the potential root causes. Use tools classified as cause analysis tools, as well as the best knowledge and experience of the team. List all possible causes for each failure mode on the FMEA form.
- For each cause, determine the occurrence rating, or O. This rating estimates the probability of failure occurring for that reason during the lifetime of your scope. Occurrence is usually rated on a scale from 1 to 10, where 1 is extremely unlikely and 10 is inevitable. On the FMEA table, list the occurrence rating for each cause.
- For each cause, identify current process controls. These are tests, procedures or mechanisms that you now have in place to keep failures from reaching the customer. These controls might prevent the cause from happening, reduce the likelihood that it will happen or detect failure after the cause has already happened but before the customer is affected.
- For each control, determine the detection rating, or D. This rating estimates how well the controls can detect either the cause or its failure mode after they have happened but before the customer is affected. Detection is usually rated on a scale from 1 to 10, where 1 means the control is absolutely certain to detect the problem and 10 means the control is certain not to detect the problem (or no control exists). On the FMEA table, list the detection rating for each cause.
- Optional for most industries: Ask, 'Is this failure mode associated with a critical characteristic?' (Critical characteristics are measurements or indicators that reflect safety or compliance with government regulations and need special controls.) If so, a column labeled “Classification” receives a Y or N to show whether special controls are needed. Usually, critical characteristics have a severity of 9 or 10 and occurrence and detection ratings above 3.
- Calculate the risk priority number, or RPN, which equals S × O × D. Also calculate Criticality by multiplying severity by occurrence, S × O. These numbers provide guidance for ranking potential failures in the order they should be addressed.
- Identify recommended actions. These actions may be design or process changes to lower severity or occurrence. They may be additional controls to improve detection. Also note who is responsible for the actions and target completion dates.
- As actions are completed, note results and the date on the FMEA form. Also, note new S, O, or D ratings and new RPNs.
FMEA Example
A bank performed a process FMEA on their ATM system. Figure 1 shows part of it: the function “dispense cash” and a few of the failure modes for that function. The optional “Classification” column was not used. Only the headings are shown for the rightmost (action) columns.
Notice that RPN and criticality prioritize causes differently. According to the RPN, “machine jams” and “heavy computer network traffic” are the first and second highest risks.
One high value for severity or occurrence times a detection rating of 10 generates a high RPN. Criticality does not include the detection rating, so it rates highest the only cause with medium to high values for both severity and occurrence: “out of cash.” The team should use their experience and judgment to determine appropriate priorities for action.
Adapted from The Quality Toolbox, Second Edition, ASQ Quality Press.